Il y a 7 années 3 mois
En 2012, sur un gisement national de déchets plastiques estimé à 3,5 millions de tonnes, seules 660 000 tonnes de déchets plastiques post-consommation et 332 000 tonnes de déchets plastiques issus des chutes de transformation étaient récupérées en vue du recyclage. Concernant les matériaux composites (plastiques associés à des renforts fibreux longs ou continus), 30 000 tonnes de déchets sont collectées sur le territoire, sans valorisation ou presque, même si des solutions techniques existent. Entretien avec Frédéric RUCH, responsable du pôle Ingénierie des Polymères et Composites au CETIM-CERMAT.
- En quelques mots, qu’est-ce que le CETIM-CERMAT ?
- Frédéric RUCH : Il s’agit d’un Centre Régional d’Innovation et de Transfert Technologique (CRITT) en mécanique avancée, membre de l’Institut Carnot MICA. Le CERMAT, pour Centre d’Études et de Recherche en Mécanique Appliquée au Textile, est né en 1977 de la volonté des entreprises mécaniciennes de la machine textile d’évaluer leur niveau de compétence. Il s’associe en 1982 au Centre Technique des Industries Mécaniques (CETIM), d’où son nom actuel.
Le 29 juin 2018, le CETIM-CERMAT devrait fusionner avec le CRITT Matériaux Alsace pour former une nouvelle entité qui s’appellera CETIM Grand Est et comptera environ 80 salariés sur les sites de Mulhouse (50 personnes), Strasbourg (25 personnes) et Metz (4 personnes).
A noter que 70% des recettes du CETIM-CERMAT (budget de 5,2 millions) proviennent de contrats industriels. En effet, chaque année, Le CETIM-CERMAT réalise 1.300 interventions auprès de 500 entreprises, majoritairement situées en d’Alsace et de Franche-Comté.
Le CETIM-CERMAT intervient sur :
- l'analyse de la défaillance des matériaux métalliques et surfaces ;
- la simulation du vieillissement des pièces et de matériaux ;
- l’élaboration et la mise au point de matériaux composites à partir de matières issues du recyclage.
Sur ce dernier point, une plateforme d’expérimentation R&D et de démonstration pré-industrielle (existant depuis fin 2016, inaugurée en octobre 2017) permet aujourd’hui la mise en oeuvre d’une solution innovante pour le recyclage des plastiques et composites thermoplastiques.
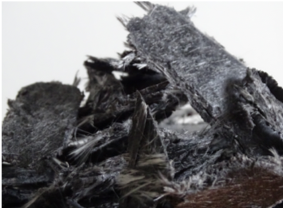
- Quels sont les enjeux liés au recyclage des composites ?
- Frédéric RUCH : Plusieurs facteurs rendent le recyclage des matériaux composites difficile :
- ce sont des matériaux hétérogènes et anisotropes (i.e. les propriétés varient selon la direction considérée) ;
- il existe une grande diversité de renforts et de matrices ;
- des charges minérales, des composants et d’autres matériaux (inserts métalliques, mousse, etc.) y sont souvent intégrés.
Par ailleurs, les matières premières de recyclage (MPR) sont confrontées à un déficit d’image et leur taux d’incorporation ne représente qu’environ 7% de la production totale de plastique en France (source : ADEME. BIO by Deloitte. Mars 2015. Bilan National du Recyclage 2003-2012 – Rapport). Le taux d’utilisation des MPR plastiques est également très dépendant du coût de la matière vierge (en corrélation avec le prix du baril de pétrole).
Actuellement, dans 90% des applications, les matériaux composites sont élaborés à partir de résines thermodurcissables. La nature même de ces résines (infusibles, une fois polymérisées), rend complexe la revalorisation du matériau en fin de vie ou des chutes de production. A noter que les procédés développés par le CETIM-CERMAT ne s’appliquent pas pour ces matériaux.
- Comment fonctionnent les procédés développés par le CETIM-CERMAT ?
- Frédéric RUCH : Les procédés développés par le CETIM-CERMAT visent la production de composites thermoplastiques à partir de matière recyclée. Pour cela l’objectif est de développer une ligne de production proposant deux systèmes d’alimentation différents :
- Procédé Thermosaïc® : revalorisation des déchets de composites thermoplastiques (ex. chutes de production), selon un principe thermo-mécanique.
- Procédé ThermoPRIME® : il s’agit d’associer des renforts de fibres longues (ex. tissu ou mat de verre), avec une matière thermoplastique issue du recyclage (ex. polypropylène ou polyamide) ;
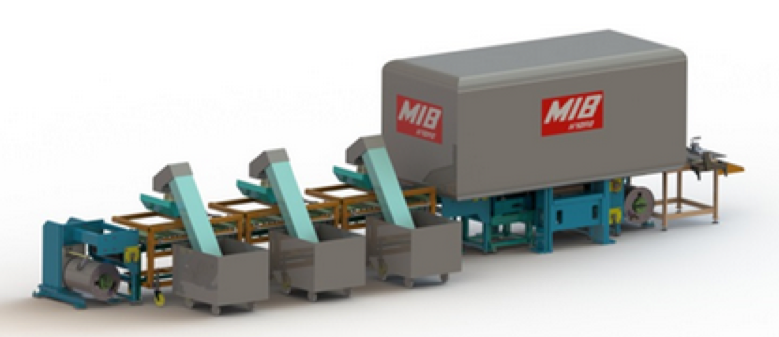
Ensuite, les produits issus des procédés Termosaïc® et ThermoPRIME®, disponibles sous forme de panneaux et de profilés, peuvent être mis en œuvre selon des techniques conventionnelles telles que l’usinage, le thermo-estampage, le soudage, etc. pour la production de pièces industrielles, en petites et moyennes séries.
Pour plus d’informations : voir la vidéo.
- Quels sont les plus-values et freins de ces procédés ?
- Frédéric RUCH : A contrario des matériaux composites thermodurs qui sont figés de façon irréversible après production, les matériaux issus de la ligne du Cetim-Cermat sont eux-mêmes recyclables par le même procédé (Termosaïc®) . La technologie s’inscrit donc dans un principe de recyclage en boucle fermée et dans la tendance de « l’upcycling ».
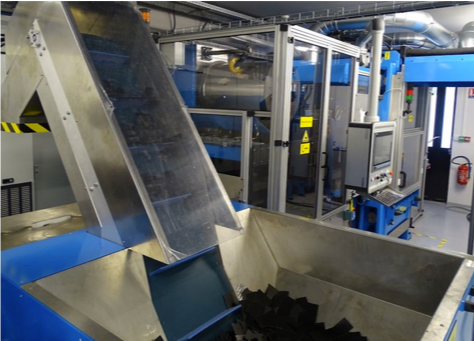
Concernant le procédé Thermosaïc®, la limite actuelle réside dans l’usage encore peu développé de ces composites, avec de faibles gisements dans des secteurs d’activités bien ciblés (automobile haute-gamme ou aéronautique) au regard du coût de ces matériaux. En effet, sur 30 000 tonnes de matériaux composites collectés en Frances, une grand majorité sont des composites thermodurs. Néanmoins, compte-tenu de leur potentiel de croissance, le but est d’anticiper la gestion des chutes de production comme de leur fin de vie.
Concernant le procédé ThermoPRIME®, le gisement de plastique recyclé existe déjà et une partie du flux actuellement orientée vers la plasturgie traditionnelle pourrait être captée pour permettre la fabrication à moindre coût de semi-produits en composite thermoplastique présentant une meilleure valeur-ajoutée.
- Quelles sont les perspectives de marché pour la ligne du CETIM-CERMAT ?
- Frédéric RUCH : Depuis les années 60, les matériaux composites ont commencé à remplacer le métal dans un nombre croissant d’applications en raison de leurs caractéristiques techniques (résistance mécanique, légèreté, tenue à la corrosion, faible coût de revient, etc.). Si la production de composites thermodurs reste majoritaire, les dernières études indiquent que le marché mondial des composites thermoplastiques progresse de plus de 5% par an et dépassera sans doute les 10 milliards de $ à l’horizon 2020.
A ce jour, la technologie du CETIM-CERMAT est en cours de développement. Sur l’échelle TRL (de anglais technology readiness level), système de mesure (de 1 à 9) employé pour évaluer le niveau de maturité d'une technologie, le pilote semi-industriel du CETIM-CERMAT se trouve au niveau 5-6.
Dans le cadre du projet ECOTREVE, le CETIM-CERMAT a travaillé avec 2 TPE/PME (PLASTIFORM + AIREPUR) pour la production de pièces de démonstrations afin de donner une idée des applications des produits. Le CETIM-CERMAT continue à travailler pour augmenter la maturité de la technologie à une échelle 7 ou 8 qui permettrait d’envisager un transfert technologique chez un industriel, avec des partenariats en cours d’élaboration.
► Pour plus d’information :
- Frédéric RUCH, Responsable Pôle IPC (Ingénierie des Polymères et Composites)
- fr [at] cetim-cermat.fr | +33 (0) 3 89 32 72 49
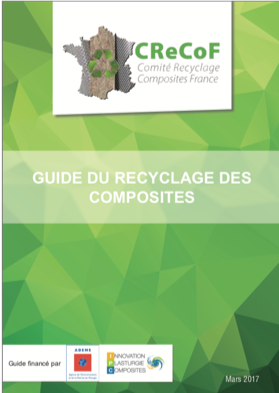
D’autres technologies, déjà commercialisées ou encore en développement, permettent le recyclage de ces composites. Elles sont répertoriées dans le Guide du recyclage des composites publié par le CRECOF avec le soutien de l’ADEME et de l’IPC (Innovation, Plasturgie, composites). Nous pouvons lister 3 technologies d’ores et déjà opérationnelles :
- La technologie du broyage ou de la micronisation permet de traiter le déchet composite par action mécanique afin d’obtenir un produit qui pourra être ré-incorporé comme renfort ou charge dans un nouveau matériau.
- La technologie de la pyrolyse fait subir au déchet composite une action thermique à haute température produisant une dégradation de la résine et une séparation des constituants. Ainsi, les fibres peuvent être récupérées à l’issue du procédé afin d’être réintroduites dans des plastiques ou composites.
- Une solution mixte (alliant recyclage et valorisation énergétique) est l’utilisation du composite dans les fours de cimenterie. Par cette voie de traitement, la partie organique du composite apporte du pouvoir calorifique tandis que la partie minérale entre dans la composition du ciment.
D’autres méthodes encore en développement semblent prometteuses :
- La vapo-thermolyse assure un transfert thermique grâce à la vapeur d’eau permettant la valorisation de fibres de carbone des déchets composites. Elle a été mise en œuvre à l’échelle industrielle pour la valorisation des pneumatiques usagés et est en développement pour l’aéronautique et l’automobile.
- Le projet RECYTAL a pour objectif de récupérer des chutes de composites biosourcés, détourées après thermocompression pour les valoriser.
- Enfin, la technologie d’alignement des fibres permet de détisser des morceaux de tissus afin de réaligner les fibres pour favoriser leur réutilisation.
Autre innovation en cours de développement, le Pôle de Plasturgie de l’Est (PPE) et Arkema développent une technologie de composites TP, compatible avec les cycles courts de l’automobile et entièrement recyclable.
Enfin, la dépolymérisation est le processus inverse de la polymérisation durant laquelle les monomères se joignent entre eux pour former des molécules plus longues, les polymères. Ainsi, les méthodes de dépolymérisation, principalement de matériaux polyéthers, polyesters et polycarbonates sont capables de recycler les déchets polymériques en molécules chimiques de bases.